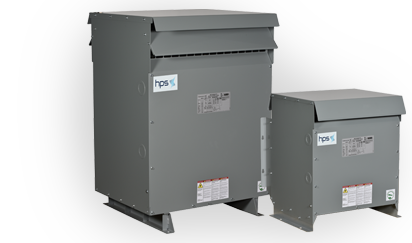
Products
HPS offers a variety of dry-type transformers, reactors, and filters that no other transformer manufacturer can match.
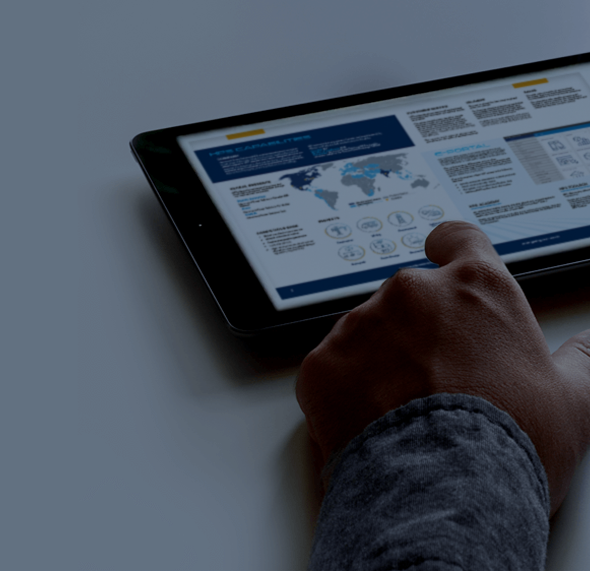
HPS Catalogs & Literature
Our HPS product brochures allow you to configure and specify the right product for your needs.
About Us
HPS is the largest manufacturer of dry-type transformers in North America. We engineer and manufacture a wide range of standard and custom transformers that are exported globally in electrical equipment and systems.
-
Renewable Energy
-
Commercial Infrastructure
-
Power Quality
-
Mining
-
Petro-Chemical
-
Manufacturing
Industries we serve
Renewable Energy
HPS builds custom transformers for alternative energy systems such as wind power and co-generation...
Industries we serve
Commercial Infrastructure
Transformers have been and remain an essential part of our electrical infrastructure. Everywhere we look there is a transformer supplying power to...
Industries we serve
Power Quality
The quality of the electricity is important to maintain critical operations, protect expensive equipment and provide inexpensive power. HPS has important products which mitigate current and voltage harmonics.
Industries we serve
Mining
The environmental conditions found in mining applications include extreme heat, cold, dust, and varying altitudes. Transformers must be...
Industries we serve
Petro-Chemical
HPS offers the broadest variety of transformer and reactor solutions for the difficult applications found...
Industries we serve
Manufacturing
HPS transformers and reactors are engineered to regulate power to conveyors, robotics, machine tools and other production-line equipment. They are rugged...
Technical Support
Leverage many tools to assist you with your technical questions: Customer Service, FAQs, Troubleshooting Guide, Installation Manuals, Instruction Sheets and Webinars.
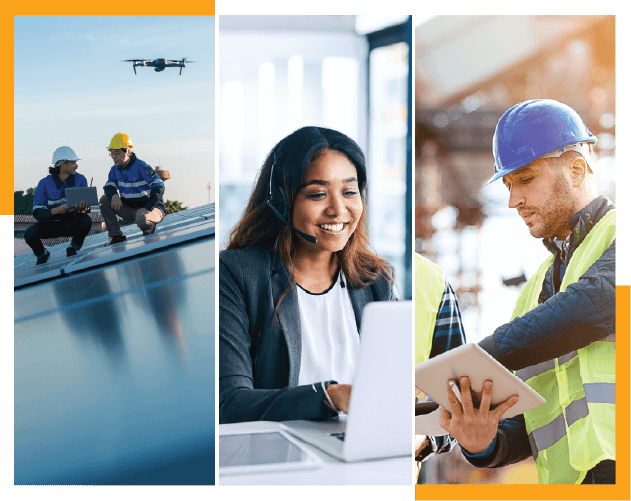